濺射靶材是電子信息產業的關鍵原材料之一,其產品質量關系到濺射薄膜的品質和濺射設備的安全。
濺射靶材種類繁多。從材質來說,包括鋁及鋁合金、銅及銅合金、鎳及鎳合金、鉻、鉬、鈦、鎢及鎢
合金、金、銀、鉑、鉭、硅、二氧化硅、氧化銦錫、二氧化錫、鐵基合金和稀土等。從靶材原始坯料
的制造方法來分,主要有熔鑄靶和粉末靶;從有無背板的角度來分,主要是焊接靶和單體靶。熔鑄靶材
的制造流程一般包括以下四步:化學提純制備高純原材料、熔煉鑄造制備鑄坯、塑性加工(鍛造、擠壓
和軋制)與熱處理、最后是機械加工。難熔金屬靶材、熔點相差很大的金屬合金靶材和陶瓷靶材坯料一般采
用粉末法制備坯料。其關鍵制造流程是:制粉、粉末冶金制坯或直接噴涂成型、對坯料進行切割、機械
加工成品。上述兩大靶坯制造流程中,除提純、制粉和機械加工外的其他制造工序都是容易產生內部缺陷
的高風險工藝。靶材內部缺陷的存在將會在濺射過程中產生顆?;蝻w濺,從而降低薄膜質量。對于焊接靶材,焊接質量關系到濺射靶材與背板之間的焊接強度和濺射過程中靶材散熱,無論是對于濺射設備安
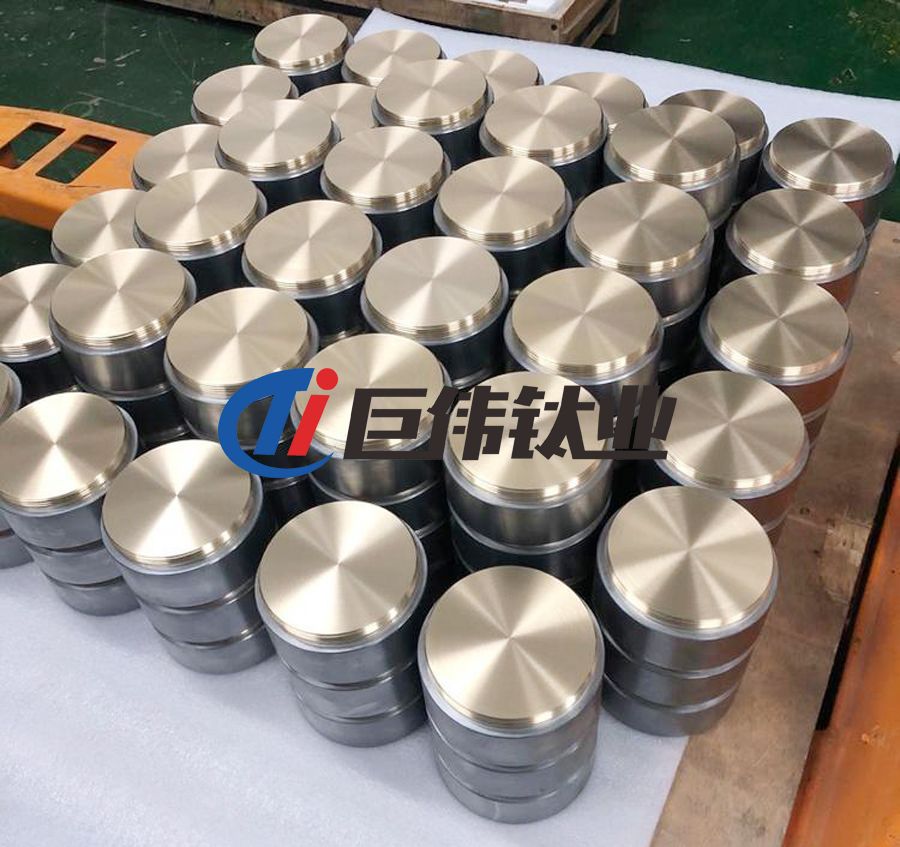
全還是濺射薄膜質量,焊接質量都是衡量濺射靶材質量是否合格的關鍵指標之一。因此,在濺射靶材的
制造過程中采用無損檢測技術成為確保制備合格濺射靶材的必要措施。
1、鑄坯與粉末冶金坯料的檢驗
靶材制造用鑄坯中的缺陷包括氣孔、夾渣、疏松和裂紋等,多是體積型缺陷。對于鋁及鋁合金靶材
來說,還存在氧化鋁顆粒的檢測問題。如果帶有缺陷的鑄坯進入制造流程中,最終的靶材可能完全不合格
。因此在下料前必須對鑄錠進行內部缺陷檢驗。X射線檢測技術和超聲波檢測技術都可以進行材料內部缺
陷檢驗,但其適用性取決于鑄坯的材質。
試驗發現,超聲波在超高純鋁及合金(>5N,99.999wt%)鑄坯中傳播時,衰減較小,也不
存在由于晶粒粗大導致的晶界散射現象。圖1所示為設計的鋁合金鑄坯對比試塊軸向截面圖和超聲
C掃圖像,檢測頻率為10MHz,探頭晶片直徑φ0.375×25.4mm,探頭焦距為4×25.4
mm。
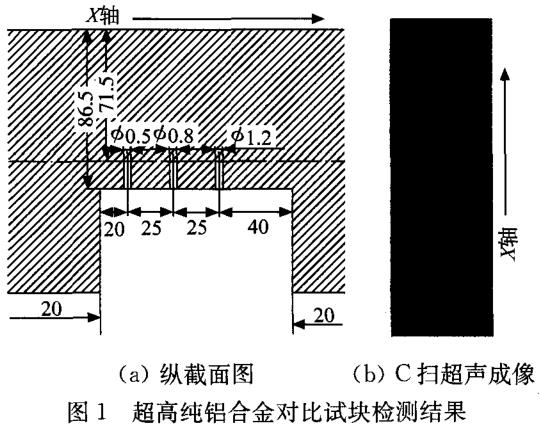
可以看出,水浸C掃超聲波技術可以有效滿足鋁及鋁合金鑄錠內0.5mm平底孔當量的缺陷
檢測要求。檢驗質量驗收標準如表1所示。
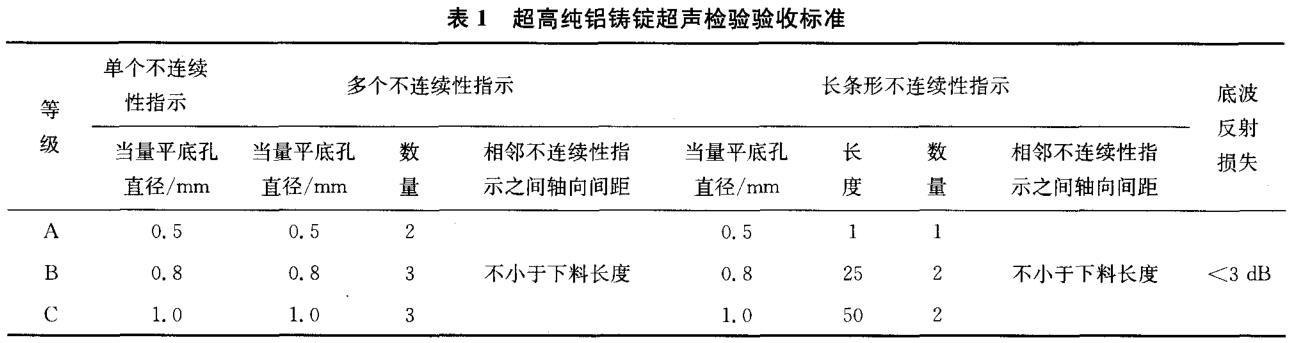
超高純銅(≥6N)鑄坯和超高純鎳(≥5N)鑄坯的晶粒尺寸巨大,都是厘米量級,主要是因為鑄
造過程中缺少型核質心導致過低的形核率而造成的。通過對兩者的鑄坯進行超聲波檢驗發現,兩者都不
適合采用超聲波檢驗技術進行內部缺陷檢驗,但其原因卻完全不同。
超聲波在超高純銅中傳播時存在兩個問題:一是衰減嚴重;二是晶體取向的影響。首先,
采用USN60超聲探傷儀和5MHz縱波直探頭,以82dB的增益檢驗上下表面平行的150mm厚鑄
錠(表面粗糙度<1.6tim)時,只能觀察到一次底波且波幅不超過滿屏的10%,表明超聲波衰減嚴
重,無法對鑄錠進行有效檢測。其次,在利用水浸C掃描技術采用2.25MHz4×25.4mm焦距探
頭對75mm厚高純銅鑄錠進行檢測時發現,檢測入射面不同區域的底波顯示的厚度與實際厚度存在
較大差別,如圖2所示。不同區域的C掃測量厚度的差異表明不同區域之間的聲速存在差別,與標準聲速相比最大
可以增大約24.56%。這種現象主要是由于鑄錠內晶粒尺寸的巨大引起的。超聲波在介質中傳播的聲速與
介質的彈性模量E有關。對于晶粒細小的多晶材料,由于晶體取向是隨機的,因此材料整體表現為各
向同性,其彈性模量也是各向同性,超聲波在其中傳播的聲速也各向相等。但對于單晶材料,其彈性模量與晶體取向有關。超聲波在晶粒粗大的超高純銅鑄錠中傳播時,實質是在不同晶粒內的傳播。各
個晶粒的取向都存在差異,由此導致了各區域聲速的不同。這種晶體取向導致聲速的差異為利用超聲
波檢測超高純銅鑄錠內部缺陷增加了新的困難。
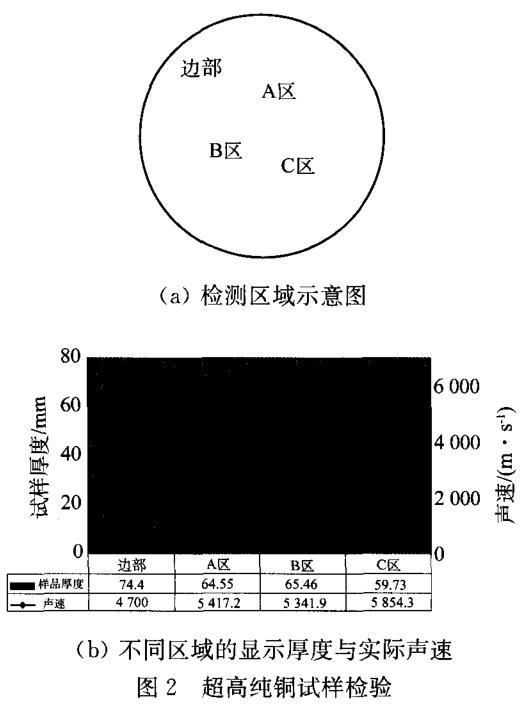
與超高純銅鑄錠明顯不同,超聲波在高純鎳中的衰減并不明顯,其主要問題是粗大晶粒導致的晶
界散射。將高純鎳鑄錠切割成薄片,表面處理后粗糙度<1.6μm。然后分別采用x射線檢測技術和
超聲波檢測技術對該切片進行檢測。對比發現兩種方法的檢驗結果并不相符,X射線判定切片中無缺陷
的區域,超聲波檢驗時判定存在缺陷。經解剖并
逐層磨制觀察,確認這些區域不存在缺陷,而是晶界,如圖3所示。說明超純鎳鑄錠中晶界散
射對超聲波檢驗存在嚴重干擾而無法進行有效判定。綜上所述,對于高純銅和高純鎳鑄錠的內部缺陷,
超聲波檢測存在局限,x射線技術更適用。
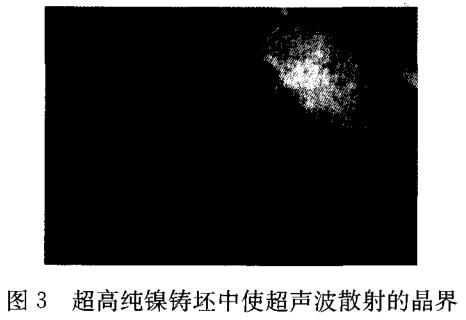
粉末法制備的靶材坯料一般超聲波聲學特征較好,且晶粒尺寸細小,因此,多數可以適用于超聲波檢測技術。
粉末法制備的坯料,無論是粉末冶金法還是噴涂法,其內部缺陷主要包括裂紋、空洞、夾雜和不致
密。與鑄錠內的球形或長條形空洞不同,粉末法坯料中的空洞和夾雜主要是不規則形狀,其形狀與夾
雜物的形狀相同。因此,空洞、夾雜和裂紋在粉末坯料中可以任意方向,必須從多個角度進行檢測才能
確保無遺漏。對于不致密則主要是觀察底波損失來判定。一般如果某區域底波損失超過4dB,即可判定
該區域不致密。
2、塑性加工靶坯的檢驗
除少數鑄造靶材和直接噴涂成型靶材外,大多數靶材都是通過一系列塑性加工和熱處理制成。塑、
性加工方法包括熱鍛、冷鍛、熱軋制、冷軋制、模壓、擠壓和拉伸等。熱處理包括固溶處理、正火
、退火、淬火和時效等。理論上每個工序后都應該進行檢驗,但考慮到生產效率,一般在加工完成后
對最終的靶材板坯進行檢驗。
經過上述工藝加工后,靶材板坯的顯微組織得到了顯著細化,板坯厚度為3~40mm
之間,超聲波聲學特征良好。在上述加工過程中,靶材板坯內可能形成的缺陷包括裂紋、分層、夾雜、
折疊、過熱、晶粒粗大、過燒、白點和疏松等。除裂紋外,這些缺陷有個共同的特征,即呈線性平
面形狀,方向沿塑性加工的流線方向,且與塑性加工平面平行。顯然,超聲波檢測技術對此類特征的缺
陷最為靈敏。因此靶材內部缺陷的檢驗與評判一般都采用超聲縱波脈沖反射式水浸C掃檢測技術。檢測
時一般將超聲波焦點聚焦到靶坯厚度的中間位置。
評判驗收標準與靶材的應用等級有關。根據驗收要求設計加工人工平底孔對比試塊即可。表2列出
了當前通用的靶材坯料內部驗收標準。
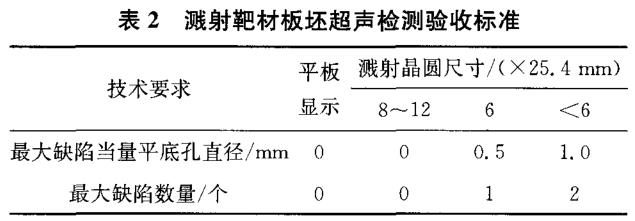
3、焊接質量檢驗
出于降低成本和增強板材組件強度和導熱性能要求,多數濺射靶材采用了與冷卻背板焊接的形式,
尤其是大尺寸靶材。濺射靶材的背板一般采用鋁合金、銅合金、鉬或者不銹鋼等,其構型有的簡單,只
是一塊具有一定硬度、強度和厚度的圓形或者矩形板材;有的構型復雜,內部帶有復雜的冷卻水道。
濺射靶材與背板的焊接是在對濺射靶材板坯完成機械加工后進行,使用的焊接技術包括釬焊、電子束
焊、擴散焊和爆炸焊等。
真空電子束焊接形成的焊縫中可能存在的缺陷有裂紋、空洞、夾雜、未熔合和未焊透等。根據使用
環境的技術要求來確定針對真空電子束焊接質量的檢驗方法。
釬焊、擴散焊和爆炸焊應用于靶材時,焊接方式基本都是兩個平面之間的焊接。釬焊是采用中間材
料將兩工件進行粘接的連接方式,中間材料(即釬焊焊料)包括銦和錫基焊料等低溫焊料。存在的焊接缺
陷主要是未粘接和夾雜。
擴散焊過程較為復雜,焊接面還要進行特殊處理,如噴砂毛化或者車齒。毛化或者車齒后的焊接界
面本身就存在著缺陷--微小尺寸的裂隙,一般為百微米量級。因此擴散焊檢測的主要是尺度較大的,
如毫米量級的未焊合。爆炸焊和擴散焊相似。
無論是釬焊、擴散焊還是爆炸焊,其焊接缺陷具有共同的特征,即線狀平面型缺陷。因此主要采用超
聲縱波C掃描技術進行檢驗和評判。
焊接檢驗用對比試塊的設計與加工技術要求可以參考ASTMF1512標準。對于釬焊來說,一般選
擇10MHz的水浸聚焦探頭進行檢驗。而對于對擴散焊,超聲波頻率的選擇則必須考慮焊接界面特征。
另外,釬焊與擴散焊的質量驗收標準也存在差別。
表3列出了釬焊和擴散焊焊接質量的驗收標準。顯然擴散焊的驗收要高于釬焊。
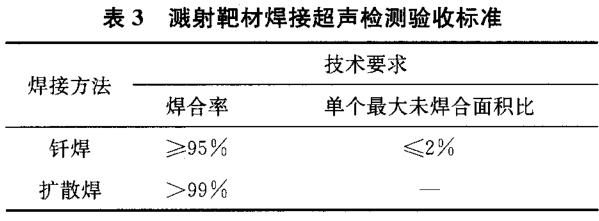
4、結語
當前X射線檢測技術和超聲波檢測技術基本可以滿足靶材制造的檢測要求。除鑄錠原材料外,超聲波
檢測技術在濺射靶材制造中應用得更為廣泛。超聲波檢測工序的安排要兼顧產品質量和生產效率。靶材板坯和焊接質量的檢驗方法主要是超聲縱波脈沖反射C掃描技術。濺射工藝的要求導致靶材檢驗的驗收
標準十分嚴格。
參考文獻:
[1]陳建軍,楊慶山,賀豐收.濺射靶材的種類、應用、制備及發展趨勢FJ].湖南有色金屬
,2006,22(04):38-76.
[2]金永中,劉東亮,陳建.濺射靶材的制備及應用研究[J].四川理工學院學報(自然科
學版),2005,18(3):22-24.
[3]努力古.濺射靶材的制備及發展趨勢[J].新疆有色金屬,2008(5):55-56.
[4]尚再艷,江軒,李勇軍,等.集成電路制造用濺射靶材[J].稀有金屬,2005,29(4):
475-477
[5]劉志堅,陳遠星,黃偉嘉,等.濺射靶材的應用及制備初探[J].南方金屬,2003,135:23-
32.
[6]WickershamCE,PooleJrJE,LeybovichA,eta1.Measurementsofthe
criticalinclusionsizeforarcingandmacroparticleejectionfromaluminumspu
tteringtargetsVJ,1.JVacSciTechnolA,2001,19(6):2767-2772.
[7]WickershamCE,PooleJrJE,FanJS.Arcgenera-tionfromsputteringplasm
a-dielectricinclusioninterae-tionsVJ].JVacSciTechnolA,2002,20(3):833-83
8.
[8]WickershamCE,PooleJrJE,FanJS,eta1.Videoanalysisofinclusionindu
cedmacroparticleemissionfromaluminumsputteringtargets[J].JVacSciTech-nolA
,2001,19(6):2741-2750.
[9]GarySSelwyn,CoreyAWeiss,FedericoSequeda,eta1.Particlecontamination
formationinmagnetronsputteringprocesses[J].JVacSciTechnolA,1997,15(4):20
23-2028.
[10]VikramPavate,MuraliAbburi,SunnyChiang,eta1.Correlationbetweenalum
inumalloysputteringtargetmetallurgicalcharacteristics[J].ArcinitiationandIn-
filmDefectDensity,1997(3214):42-47.
[11]PaulSGilman,AlfredSnowman,AndreDesert.De-terminationofactu
aldefectsizeincathodesputtertargetssubjectedtoultrasonicinspection:US,
6269699B1EP].2001.
[12]CharlesEWickersham,JohnEPoole,AlexanderLeybovich,eta1.Methodfor
determingacriticalsizeofaninclusioninaluminumoraluminumalloysputte-
ringtarget:US,7087142B2[P].2006.
[13]CharlesEWlckershamJR,JohnEPoole,AlexanderLeybovich,eta1.Methodfo
rdetermingacriticalsizeofaninclusioninaluminumoraluminumalloysputte-
ringtarget:US,2004/0118675AI[P].2004.
[14]RussellBGore,RonaldHFleming.Methodsoftes-tingsputteringtargetm
aterials:US,6439054B1[-P1.2002.
[15]CharlesEWlckershamJR,JohnEPoole,AlexanderLeybovich,eta1.S
puttertargetsandmethodsofmanufacturingsametoreducep[
[16]HidemasaTamura,NorioYokoyama,EiichiShimi-ZU,eta1.Sputtering
targetandproductionmethodthereof:US,6024852[P,1.2000.
[17]陳岳軍,趙海燕,史耀武.粗晶材料超聲檢測缺陷信號增強的小波分析法[J].中國有
色金屬學報,1997,7(2):94-96.
相關鏈接